The Power Etching process must be performed on bare or untreated metal surfaces. Typically deep etching
your text/image and then applying your coating overtop that surface leaves a very visible and readable mark.
There are other options for the marking of coated or painted surfaces, please feel free to contact us about
our laser marking services with CO2, Yag and Fiber lasers.
Our Electrolytic etching systems run on a standard AC electrical outlet and have a current draw of 1, 5 and 8 amps maximum. The units will not exceed the fused current rating and will work on most standard AC outlets
in conjunction with other equipment on the same circuit.
Condensed Version
These units are very simple to operate and are electronically controlled and use a small amount of electric current with AC or DC voltage, an electrolyte, a carbon marker with felt pad (hold electrolyte), and a stencil containing a image/text to be marked. The power unit supplies AC/DC power to the carbon head and though
the felt pad containing etching solution transfers power to the part though the stencils image and creates a permanent mark on the part.
Detailed Version
Electrolytic etching begins with the creation of an image on a stencil. The stencil has a coating applied that blocks the marking process in areas that there is no text or image. Only the area where the text/image resides can pass liquid through the stencils from the units carbon marking head to the metals surface.
The stencil is placed on a metal surface with an electrolyte to help in the transfer of current. The electric current passes through the text/image openings in the stencil from the carbon marking head to the metal material. The electrolyte allows the text/image on the stencil to be etched into or onto the base metals surface.
The power units has one of its cables connected to the carbon marking head and the other cable is connected to the metal parts surface with a alligator style mechanical clamp to create a electrical circuit.
The carbon head power power lead and the part marking power lead are connected back to the CanEtch C100, C200 or C300 unit.(C100 photo shown below)
The marking head has a carbon bottom (conductivity) and has a metal rod mounted into the center of the carbon that is used to connect the power units electrical wire.
The carbon marking head uses a thick felt type pad to allow for electrolytic marking solution to be absorbed and retained in the etching pad. The blue side of the etching pad goes toward the carbon marking head and the white felt side is applied to the stencil surface. This pad is secured to the carbon marking head via a O-ring.
The carbon marking head with felt pad applied and soaked in the specific electrolytic marking solution for that application is then place on the parts surface ontop of the stencil image while AC or DC power is applied and creates a circuit loop where the surface of the part becomes marked.
Additional Information
The basic equipment includes a power etching unit, which provides the AC/DC voltage and enough current to etch a mark on the metal. The size of the power unit depends on the area that needs to be marked, if a small stencil is used then the smaller of the three etching unit can be used. For the larger stencils or deep etch marking one of the two higher current power etching units would be required. Also another aspect of the marking process is the marking time cycle, if you require a shorter marking time for higher production levels then a higher powered etching unit would be an advantage as marking times would be reduced.
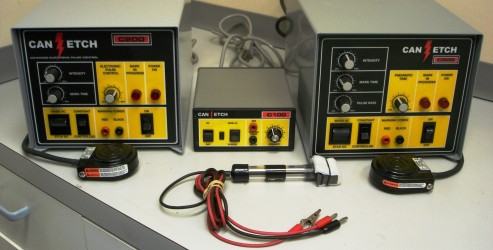
Most Power Etching units on the market today range from 5 – 40 Volts and have an ampere output from 0.1 to 8 amps. All our Power Etching units have an On-Off switch and an AC-DC switch with a variable power output dial to control mark depth and mark contrast.
Our C200 & C300 Power Etching units have digital pulse control that will allow for deep marking of materials to a few thousands deep or even to help create a darker contrasting image on your metal parts. The transformer in the Power Etching unit acts like a large capacitor and can store greater potential energy if its output is pulsed over a duration of the marking time. The transformer in the unit act like a large capacitor and can hold high peek potential energy that is released each time the output it pulsed on and off again. The pulse duration dial on these larger capacity etching units can be controlled and allow for greater marking depth or darker contrast with this special addded feature.
The Power Etching units also have a mark duration timer along with a start mark foot pedal that allows the operator to start the marking cycle with their foot. In conjunction with the marking duration timer the operator can dial in the exact marking time needed to achieve a constant uniform and repeatable mark between parts. The mark duration timer will apply power to the carbon marking head for the exact amount of time each time the foot pedal is depressed increasing the conformity of the marks.
North American Marking Solutions Inc | 27 Strathearn Ave Unit 5 Brampton Ontario L6T 4V5 | 416-620-1515